How 3D Printing Is Disrupting Manufacturing
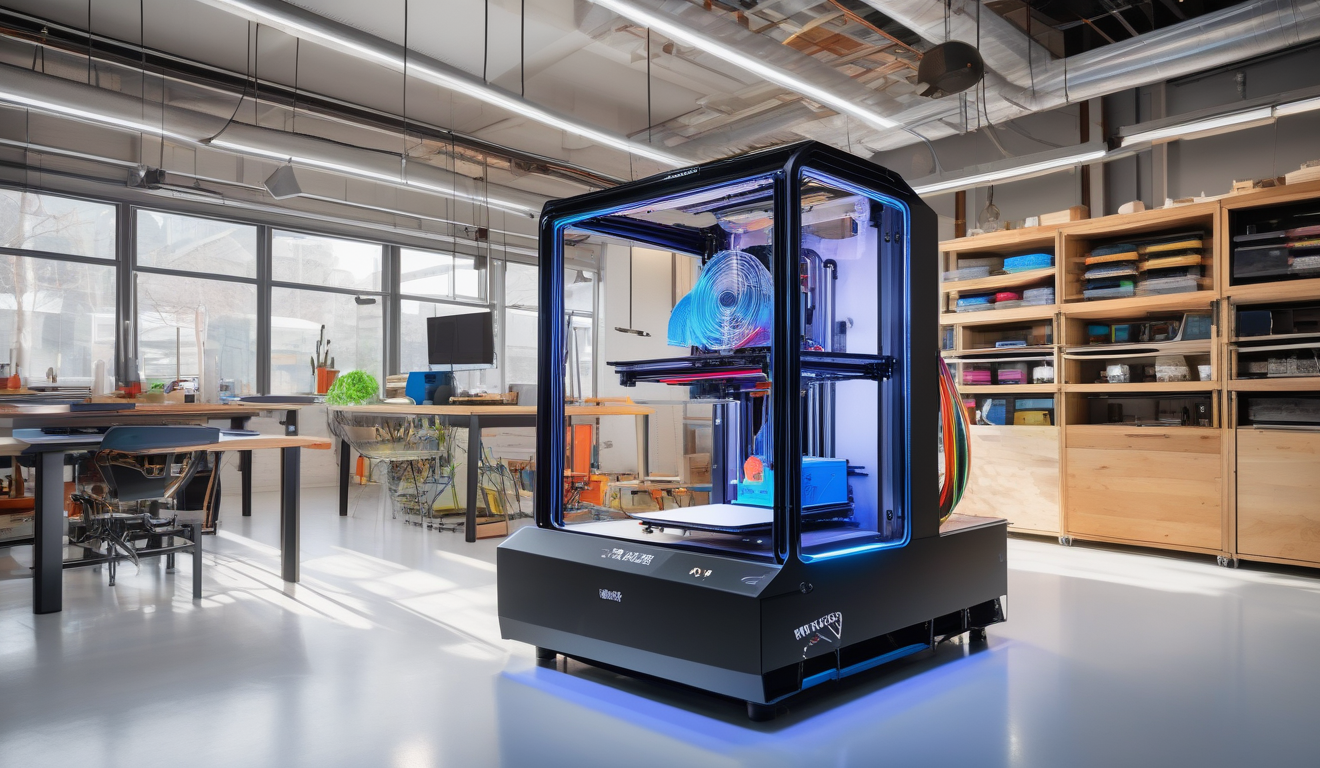
3D printing, often referred to as additive manufacturing, is not just a buzzword—it’s a revolution that is reshaping the manufacturing landscape. This technology, which allows for the creation of three-dimensional objects from digital files, has gained immense traction in recent years. But what does this mean for the traditional manufacturing processes we’ve relied on for decades? Let’s dive in!
Imagine a world where you can create complex parts in a fraction of the time it takes with conventional methods. That’s the promise of 3D printing! Initially developed in the 1980s, this technology has evolved dramatically, thanks to advancements in materials, software, and printing techniques. Today, industries ranging from aerospace to healthcare are embracing 3D printing, recognizing its potential to not only streamline production but also to foster innovation.
One of the most compelling aspects of 3D printing is its cost-effectiveness. Traditional manufacturing often involves significant overhead costs related to tooling and material waste. In contrast, 3D printing minimizes these expenses by using only the material necessary for production. This means manufacturers can allocate their resources more efficiently, leading to improved profit margins. For example, a study revealed that companies utilizing 3D printing saw a reduction in material waste by up to 90% compared to traditional methods.
Moreover, the design flexibility offered by 3D printing is a game-changer. Designers can create intricate geometries and customized products that were previously unimaginable. This opens up a world of possibilities, allowing for tailored solutions that meet specific customer needs. In essence, 3D printing is not just about making things faster; it’s about making things better.
However, it’s essential to acknowledge the challenges that come with integrating this technology into existing manufacturing processes. From technical limitations to regulatory hurdles, manufacturers must navigate a complex landscape to fully harness the benefits of 3D printing. Yet, the potential rewards make it a journey worth undertaking.
As we look to the future, the integration of 3D printing with Industry 4.0 principles promises to usher in a new era of smart manufacturing. This synergy could lead to unprecedented levels of efficiency and innovation in production processes. It’s clear that 3D printing is not just a trend; it’s a fundamental shift in how we think about manufacturing.
The Rise of 3D Printing Technology
The journey of 3D printing technology is nothing short of fascinating. It all began in the 1980s when the first 3D printer was developed by Chuck Hull. Hull’s invention, known as stereolithography, laid the groundwork for what would become a revolutionary manufacturing process. Fast forward to today, and we’ve witnessed incredible advancements that have transformed 3D printing from a niche technology into a mainstream manufacturing solution.
Several factors have contributed to the growing adoption of 3D printing across various sectors. One major driver is the rapid evolution of materials. Initially, 3D printing was limited to a handful of plastic types, but now manufacturers can choose from a wide array of materials, including metals, ceramics, and even bio-materials. This expansion allows for greater versatility and opens up new possibilities for product development.
Moreover, the decrease in costs associated with 3D printing technology has made it accessible to smaller businesses and startups. As prices for 3D printers and materials continue to drop, more companies are realizing the benefits of integrating this technology into their production processes. This shift is not just about affordability; it’s also about speed. Traditional manufacturing methods can take weeks or even months to bring a product from concept to market. In contrast, 3D printing can significantly reduce this time frame, allowing businesses to respond quickly to market demands.
Another key factor is the rise of the digital age. With the advent of advanced software and design tools, creating complex models has never been easier. Designers can now experiment with intricate shapes and structures that were previously deemed impossible. This newfound design flexibility fosters innovation, enabling companies to differentiate themselves in a competitive marketplace.
In summary, the rise of 3D printing technology is a perfect storm of innovation, affordability, and digital integration. As we continue to explore its potential, one can only imagine how it will further disrupt traditional manufacturing practices. The next chapter in 3D printing is just beginning, and it promises to be as exciting and transformative as its inception.
Benefits of 3D Printing in Manufacturing
When you think about manufacturing, what comes to mind? Long assembly lines, massive machinery, and a whole lot of waste, right? Well, 3D printing is flipping the script on traditional manufacturing methods. This innovative technology is not just a passing trend; it’s a game changer that brings a myriad of benefits to the table. From cost-effectiveness to design flexibility, 3D printing is reshaping how products are made and delivered.
One of the standout advantages of 3D printing is its cost-effectiveness. Traditional manufacturing often involves significant upfront costs for materials and tooling. However, with 3D printing, manufacturers can produce items layer by layer, which drastically cuts down on material waste. Imagine being able to create a product with only the exact amount of material needed—this not only saves money but also contributes to a more sustainable approach to production.
Moreover, the design flexibility offered by 3D printing is nothing short of revolutionary. Unlike conventional methods, which can be limited by tooling and manufacturing constraints, 3D printing allows for the creation of complex geometries that were previously thought impossible. Designers can experiment with intricate shapes and customizations, leading to innovative products that stand out in the market. This kind of flexibility means that businesses can respond faster to consumer demands and trends.
But wait, there’s more! The time-to-market is significantly reduced with 3D printing. In a world where speed is king, being able to prototype and produce items quickly gives manufacturers a competitive edge. They can bring their ideas to life in a fraction of the time it would take through traditional methods. This rapid production cycle not only satisfies consumer cravings but also allows companies to test and iterate on designs more efficiently.
Lastly, while we’re on the subject of efficiency, let’s talk about labor costs. Automation in 3D printing means that less manual labor is required, which translates to lower operational costs. Manufacturers can allocate their workforce to more critical tasks that require human creativity and problem-solving skills, thus enhancing overall productivity.
In summary, the benefits of 3D printing in manufacturing are immense. It’s not just about making things faster; it’s about making them smarter and more sustainable. As this technology continues to evolve, it will undoubtedly pave the way for a new era in manufacturing.
Cost Reduction Strategies
In today’s fast-paced manufacturing world, cost reduction is a crucial factor for businesses striving to stay competitive. One of the most significant advantages of 3D printing is its ability to minimize expenses across various stages of production. By adopting 3D printing technology, manufacturers can significantly reduce material waste, which is a common issue in traditional manufacturing processes. Imagine a sculptor who chisels away at a block of marble, creating dust and debris with every strike. Now, picture a 3D printer, which only uses the exact amount of material needed to create a part, leaving virtually no waste behind. This shift not only conserves resources but also translates to substantial savings on raw materials.
Moreover, 3D printing allows for efficient resource allocation. By lowering production costs, manufacturers can redirect funds to other critical areas of their business, such as research and development or marketing. This flexibility can lead to enhanced innovation and product offerings, ultimately benefiting the company’s bottom line. For instance, a business that traditionally spent thousands on excess materials can now invest in developing new products or improving existing ones, fostering a culture of creativity and growth.
Another key aspect of cost reduction is the lower labor costs associated with 3D printing. As automation becomes increasingly prevalent, the reliance on manual labor diminishes. This shift not only reduces operational costs but also streamlines production processes. Manufacturers can operate with fewer employees, allowing them to allocate their workforce to more strategic roles that require human oversight and expertise. The result? A leaner operation that can adapt quickly to market demands without the overhead of a large workforce.
To summarize the impact of cost reduction strategies through 3D printing, consider the following table:
Strategy | Description | Benefits |
---|---|---|
Material Efficiency | Utilizes only the necessary amount of material. | Reduces waste and material costs. |
Labor Cost Reduction | Automation decreases the need for manual labor. | Lowers operational costs and improves efficiency. |
Resource Allocation | Allows for better distribution of financial resources. | Encourages innovation and growth opportunities. |
In conclusion, the integration of 3D printing into manufacturing not only drives down costs but also opens up a world of possibilities for efficiency and innovation. By embracing these technologies, manufacturers can position themselves for success in an ever-evolving industry.
Material Efficiency
When it comes to manufacturing, is a game changer, and 3D printing is leading the charge. Traditional manufacturing methods often result in significant waste, where excess materials are cut away and discarded. In contrast, 3D printing, also known as additive manufacturing, builds objects layer by layer, using only the material necessary to create the final product. This not only minimizes waste, but it also promotes a more sustainable approach to production.
Imagine sculpting a statue from a block of marble. Every chip and cut can lead to waste, but with 3D printing, you’re essentially growing the statue from the ground up, using just the right amount of material. This precision is a hallmark of 3D printing technology, allowing manufacturers to optimize their resources effectively. By reducing the amount of raw materials needed, companies can not only save money but also reduce their environmental footprint.
Furthermore, the range of materials that can be used in 3D printing is expanding rapidly. From plastics to metals, and even bio-materials, the versatility of 3D printing opens up new avenues for innovation. For instance, the use of recycled materials in 3D printing processes can further enhance material efficiency. Manufacturers can now utilize waste products to create new items, effectively closing the loop in the production cycle.
Here’s a quick look at how 3D printing enhances material efficiency:
- Reduced Waste: Only the necessary amount of material is used, minimizing scrap.
- Recyclability: Many 3D printing materials can be recycled, contributing to sustainability.
- Customization: Tailored designs mean that less material is used for prototypes and final products.
In summary, the material efficiency offered by 3D printing not only leads to cost savings but also supports a more sustainable manufacturing process. As the technology continues to evolve, we can expect even greater advancements in how materials are utilized, further transforming the landscape of manufacturing.
Lower Labor Costs
One of the most compelling advantages of integrating 3D printing into the manufacturing process is the significant reduction in labor costs. Traditionally, manufacturing has relied heavily on human labor for assembly, quality control, and other essential tasks. However, with the advent of 3D printing technology, many of these roles can be minimized or even eliminated altogether. Imagine a factory floor where machines do the heavy lifting, allowing human workers to focus on more strategic and creative tasks. This not only enhances productivity but also leads to substantial savings.
By automating production through 3D printing, manufacturers can reduce the number of employees needed for repetitive tasks. For instance, a conventional assembly line may require dozens of workers to put together a single product. In contrast, a 3D printer can produce that same product with minimal human intervention. This shift not only cuts down on labor costs but also mitigates risks associated with human error, leading to higher quality outputs.
Moreover, the savings on labor can be redirected towards innovation and development. Companies can invest in research and development to create new products or improve existing ones. This reinvestment can lead to a competitive edge in the market. Here’s a quick breakdown:
Traditional Manufacturing | 3D Printing |
---|---|
High labor costs | Reduced labor needs |
Manual assembly prone to errors | Automated production with precision |
Limited flexibility | Quick adjustments to designs |
Longer production times | Faster prototyping and production |
In summary, the associated with 3D printing not only streamline operations but also create opportunities for manufacturers to innovate and thrive in an increasingly competitive landscape. As companies continue to adopt this technology, the shift in labor dynamics will likely redefine the manufacturing industry as we know it.
Design Flexibility and Innovation
When it comes to 3D printing, one of the most exciting aspects is its incredible design flexibility. Imagine being able to create shapes and structures that were once thought to be impossible. Traditional manufacturing often confines designers to specific shapes and materials, but with 3D printing, the sky is the limit! This technology allows for the production of complex geometries that can be tailored to meet the exact specifications of a project. It’s like having a magic wand that can conjure up anything your imagination dreams of.
Moreover, the innovation doesn’t stop there. Designers can experiment with customized products that perfectly fit individual needs. From personalized medical implants to bespoke fashion items, the possibilities are endless. This level of customization not only enhances user experience but also opens up new markets for manufacturers. Think about it: a shoe that molds to your foot perfectly or a piece of furniture designed specifically for your living space. This is the future that 3D printing is paving the way for.
Another significant advantage is the ability to iterate designs quickly. In traditional manufacturing, making changes can be time-consuming and costly. However, with 3D printing, adjustments can be made on the fly, allowing for rapid prototyping. This means that a company can test a design, gather feedback, and refine it almost instantaneously. It’s like having a fast track to innovation!
To illustrate the impact of design flexibility, consider the following table that compares traditional manufacturing processes to 3D printing:
Aspect | Traditional Manufacturing | 3D Printing |
---|---|---|
Design Complexity | Limited | Unlimited |
Customization | Challenging | Easy |
Time to Market | Long | Short |
Material Waste | High | Low |
In summary, the design flexibility offered by 3D printing is revolutionizing how products are conceived and manufactured. It empowers designers to push boundaries, encourages innovation, and ultimately leads to more efficient and tailored solutions. As this technology continues to evolve, we can expect even more groundbreaking developments that will redefine the manufacturing landscape.
Challenges Facing 3D Printing Adoption
While the promise of 3D printing is captivating, the journey to widespread adoption is not without its hurdles. Manufacturers face a variety of challenges that can impede the integration of this innovative technology into their operations. Understanding these obstacles is crucial for businesses looking to leverage 3D printing’s potential.
One of the primary issues is technical limitations. Despite significant advancements, current 3D printing technologies still grapple with certain constraints. For instance, the range of materials suitable for 3D printing is somewhat limited compared to traditional manufacturing methods. This can restrict designers and engineers from fully realizing their creative visions. Additionally, speed remains a concern; while 3D printing can produce complex parts, the time taken to print large quantities can be a bottleneck for manufacturers needing rapid production.
Another significant challenge lies in the regulatory and compliance issues surrounding 3D printing. As this technology evolves, so too does the need for updated safety standards and regulations. Manufacturers must navigate a complex landscape of laws that govern everything from material safety to intellectual property rights. For example, the question of who owns the design of a 3D-printed item can lead to legal complications, making manufacturers hesitant to fully embrace the technology.
Moreover, there is the market acceptance factor. Many industries are traditionally steeped in established practices and may be resistant to change. Convincing stakeholders of the benefits of 3D printing requires a cultural shift, where the value of innovation and flexibility is recognized over the comfort of traditional methods. This transition can be slow and requires education and demonstration of successful use cases.
In summary, while the potential for 3D printing in manufacturing is enormous, overcoming these challenges is essential for its successful adoption. Manufacturers must invest in research and development to address technical limitations, stay abreast of regulatory changes, and promote a culture that embraces innovation. Only then can they fully harness the power of 3D printing to transform their operations.
Technical Limitations
While 3D printing is revolutionizing the manufacturing landscape, it isn’t without its challenges. One of the most significant hurdles is the that manufacturers face when trying to implement this innovative technology. For instance, the range of materials suitable for 3D printing is still relatively narrow compared to traditional manufacturing methods. Many industries rely on specific materials that may not yet be compatible with 3D printing processes, which can limit creativity and functionality.
Moreover, the speed of 3D printing can be a bottleneck in production. While it excels in creating intricate designs, the process can be considerably slower than traditional manufacturing techniques, especially for high-volume production runs. This discrepancy raises a crucial question: how can manufacturers balance the need for speed with the benefits of customization? It’s a tightrope walk that requires careful planning and execution.
Additionally, the quality control in 3D printing presents another layer of complexity. Variability in printer settings, material quality, and environmental conditions can lead to inconsistencies in the final product. Manufacturers must invest in rigorous testing and quality assurance processes to ensure that each item produced meets the required standards. This can add to the overall costs and time associated with production.
To further illustrate these challenges, consider the following table that outlines some of the primary technical limitations of 3D printing:
Limitation | Description |
---|---|
Material Variety | Limited range of materials available for 3D printing compared to traditional methods. |
Production Speed | Slower than conventional manufacturing for large-scale production. |
Quality Control | Inconsistencies in product quality due to various influencing factors. |
In conclusion, while 3D printing holds immense potential, manufacturers must navigate these technical limitations carefully. Addressing these challenges will be crucial for the widespread adoption of 3D printing in the manufacturing sector. By investing in research and development, and by pushing the boundaries of current technology, the industry can pave the way for a more efficient and innovative future.
Regulatory and Compliance Issues
As the innovative world of 3D printing continues to grow, it faces a myriad of regulatory and compliance challenges that can significantly impact its adoption in the manufacturing sector. These challenges stem from the rapid pace of technological advancement, which often outstrips the ability of regulatory bodies to keep up. Manufacturers must navigate a complex landscape of laws and guidelines that vary not only by country but also by industry.
One of the primary concerns revolves around safety standards. As 3D printing technology evolves, so do the materials and processes involved. Ensuring that these new materials are safe for consumer use is paramount. For instance, the use of certain plastics or metals in consumer products must comply with health and safety regulations. This can lead to extensive testing and certification processes that can delay time-to-market.
Moreover, intellectual property (IP) issues pose significant risks. With the ability to replicate complex designs, 3D printing raises questions about copyright infringement and patent violations. Manufacturers must be vigilant in protecting their designs while also respecting the rights of others. This often requires a legal framework that is still being developed, leading to uncertainty in the market.
In addition to safety and IP concerns, the regulatory environment can also affect import and export restrictions. Countries may have different regulations regarding the importation of 3D printed goods, which can complicate international trade. Manufacturers looking to expand their market reach must be aware of these regulations to avoid costly penalties or disruptions in their supply chains.
To illustrate the complexity of these issues, consider the following table that highlights the key regulatory areas manufacturers must address:
Regulatory Area | Challenges | Implications |
---|---|---|
Safety Standards | Material compliance, consumer safety | Increased testing costs, potential delays |
Intellectual Property | Patent infringement, copyright issues | Legal disputes, market uncertainty |
Trade Regulations | Import/export restrictions | Supply chain disruptions, compliance costs |
In conclusion, while the potential of 3D printing is immense, the path forward is fraught with regulatory hurdles. Manufacturers must stay informed and adaptable, ensuring they comply with the evolving landscape to harness the full potential of this groundbreaking technology.
The Future of 3D Printing in Manufacturing
The future of 3D printing in manufacturing is not just bright; it’s positively dazzling! As we look ahead, it’s clear that this technology is poised to revolutionize the industry in ways we can only begin to imagine. With advancements in materials, speed, and integration with other technologies, 3D printing is set to become a cornerstone of modern manufacturing.
One of the most exciting trends is the integration of 3D printing with Industry 4.0 principles. This means that manufacturers will leverage data-driven processes and interconnected systems to enhance production efficiency. Imagine a factory where machines communicate seamlessly, adjusting their operations in real-time based on data analytics. This synergy will not only streamline processes but also lead to improved product quality and reduced downtime.
Moreover, the potential market growth for 3D printing is staggering. According to recent forecasts, the global 3D printing market could reach $34.8 billion by 2024. This explosive growth is driven by increasing demand for customized products, rapid prototyping, and the need for sustainable manufacturing practices. As more companies recognize the benefits of 3D printing, we can expect to see a wider adoption across various sectors, including aerospace, automotive, and healthcare.
However, the journey isn’t without its bumps. Manufacturers must navigate challenges such as regulatory compliance and intellectual property concerns. These hurdles can slow down the adoption of 3D printing technologies. Yet, with proactive strategies and collaboration among industry stakeholders, these challenges can be addressed effectively.
In conclusion, the future of 3D printing in manufacturing is filled with opportunity and innovation. As technology continues to evolve, manufacturers who embrace these changes will not only stay competitive but also lead the charge in creating a more efficient, sustainable, and customized production landscape. The question isn’t if 3D printing will change manufacturing, but rather how quickly and profoundly it will do so!
Integration with Industry 4.0
As we plunge deeper into the era of Industry 4.0, the integration of 3D printing is proving to be a game-changer for manufacturers worldwide. Imagine a world where machines not only communicate with each other but also adapt and learn from the data they collect. That’s the essence of Industry 4.0, and 3D printing fits right into this innovative puzzle, enhancing efficiency and productivity in ways we never thought possible.
One of the most exciting aspects of this integration is the ability to create a smart manufacturing ecosystem. With 3D printing, manufacturers can utilize real-time data to optimize production processes. For instance, data collected from printers can be analyzed to predict maintenance needs, thereby minimizing downtime. This not only saves time but also significantly reduces operational costs.
Moreover, the synergy between 3D printing and Industry 4.0 fosters a new level of customization. Manufacturers can swiftly respond to market demands by altering designs on-the-fly, producing tailored products without the lengthy lead times associated with traditional manufacturing. This agility is crucial in today’s fast-paced market, where consumer preferences can shift overnight.
Additionally, the integration of Internet of Things (IoT) technologies with 3D printing allows for enhanced monitoring and control. Imagine being able to track the performance of each printed part in real-time, ensuring quality and consistency. This capability not only boosts productivity but also enhances the overall quality of the final products.
To illustrate the impact of this integration, consider the following table highlighting key benefits:
Benefit | Description |
---|---|
Increased Efficiency | Real-time data analytics streamline production processes. |
Customization | Rapid design modifications to meet market demands. |
Quality Control | Enhanced monitoring ensures consistent product quality. |
In conclusion, the integration of 3D printing with Industry 4.0 is not just a trend; it’s a revolution. As manufacturers embrace this technology, they unlock new levels of innovation and efficiency, paving the way for a manufacturing landscape that is more responsive, sustainable, and capable of meeting the challenges of tomorrow.
Potential Market Growth
The 3D printing market is on the brink of a major breakthrough, and the numbers are nothing short of astonishing. According to recent studies, the global market for 3D printing is expected to grow from $12 billion in 2021 to over $34 billion by 2026. This explosive growth is fueled by a combination of factors that are reshaping the manufacturing landscape.
One of the primary drivers of this growth is the increasing demand for customized products. Consumers are no longer satisfied with one-size-fits-all solutions; they crave personalized items that reflect their individual tastes and needs. 3D printing provides a unique solution by allowing manufacturers to produce bespoke products efficiently and at a lower cost.
Moreover, the integration of 3D printing into industries such as healthcare, automotive, and aerospace is paving the way for new applications that were once deemed impossible. For instance, in the healthcare sector, 3D printing is revolutionizing the production of prosthetics and implants, offering tailor-made solutions that enhance patient outcomes.
As the technology advances, we can expect to see a shift towards more sustainable manufacturing practices. 3D printing minimizes waste and optimizes material usage, which not only lowers costs but also aligns with the growing consumer demand for environmentally friendly products. This trend is becoming increasingly important as businesses strive to meet regulatory requirements and consumer expectations regarding sustainability.
To illustrate the projected growth, consider the following table:
Year | Market Size (in Billion $) | Growth Rate (%) |
---|---|---|
2021 | 12 | – |
2023 | 20 | 66.67 |
2026 | 34 | 70.00 |
In conclusion, as we look to the future, the 3D printing market is poised for remarkable expansion. With technological advancements, increasing customization demands, and a shift towards sustainability, the potential for growth is immense. Manufacturers who embrace this change will not only enhance their operational efficiency but also position themselves at the forefront of a manufacturing revolution.
Frequently Asked Questions
- What is 3D printing and how does it work?
3D printing, also known as additive manufacturing, is a process that creates three-dimensional objects by layering materials based on digital models. It works by using a computer-aided design (CAD) file, which is sliced into thin horizontal layers, and then a printer deposits material layer by layer until the object is complete. It’s like baking a cake, where each layer adds to the final product!
- What are the main benefits of using 3D printing in manufacturing?
3D printing offers several advantages, including cost-effectiveness, design flexibility, and reduced time-to-market. It minimizes material waste and allows for rapid prototyping, enabling manufacturers to innovate quickly and efficiently. Imagine being able to create complex designs that were once impossible with traditional methods!
- What challenges do manufacturers face when adopting 3D printing?
While 3D printing has many benefits, manufacturers encounter challenges such as technical limitations, like material constraints and production speed, and regulatory issues, including compliance with safety standards. It’s a bit like learning to ride a bike; there are bumps along the way, but with practice, it becomes easier!
- How is 3D printing expected to evolve in the future?
The future of 3D printing looks promising, with trends pointing towards greater integration with Industry 4.0 principles. This means more data-driven processes and interconnected systems, which could enhance efficiency and innovation in manufacturing. Think of it as upgrading from a flip phone to a smartphone!
- Can 3D printing help reduce environmental impact?
Absolutely! 3D printing is known for its material efficiency, which leads to less waste compared to traditional manufacturing. This sustainability aspect makes it a great choice for eco-conscious manufacturers looking to reduce their carbon footprint.