How AI-Powered Robots Are Changing Manufacturing
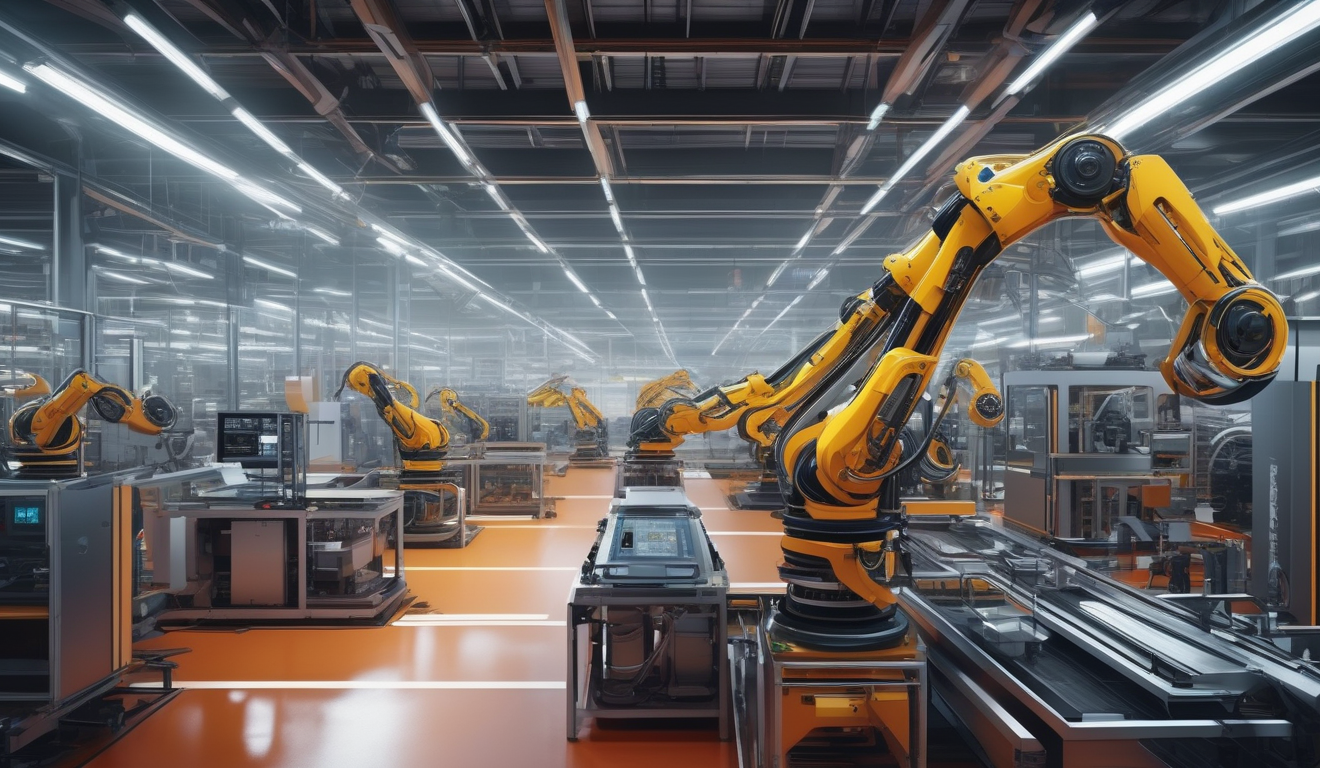
The manufacturing industry is undergoing a seismic shift, and at the forefront of this transformation are AI-powered robots. These technological marvels are not just tools; they are revolutionizing how products are made, how factories operate, and how businesses thrive in a competitive landscape. Imagine a world where machines work tirelessly alongside humans, enhancing productivity and precision—this is not science fiction but the reality of modern manufacturing.
As we delve into this fascinating topic, it’s essential to understand that the integration of AI into manufacturing is driven by several key factors. First off, the demand for faster production times and higher quality products is skyrocketing. Consumers expect nothing less than perfection, and businesses are rising to the challenge. AI robots are stepping in to meet these expectations, optimizing every aspect of the manufacturing process. With their ability to analyze data and adapt to changing conditions, these robots are becoming indispensable.
But what exactly are the benefits of incorporating AI-powered robots into manufacturing? For starters, they offer enhanced precision that human workers simply cannot match. Imagine a robot that can assemble tiny components with pinpoint accuracy—this level of detail not only improves product quality but also reduces waste. Moreover, the cost savings associated with reduced labor needs and minimized errors are significant, allowing companies to allocate resources more effectively.
Furthermore, AI robots are designed to take over repetitive tasks, freeing up human workers to engage in more complex and fulfilling roles. This shift not only boosts overall productivity but also enhances employee satisfaction, as workers can focus on tasks that require creativity and critical thinking. In essence, AI is not here to replace jobs but to transform them.
As we look to the future, the landscape of AI in manufacturing continues to evolve. Emerging trends such as collaborative robots (cobots) and predictive maintenance are set to redefine operational efficiency. Cobots work alongside humans, enhancing productivity without the fear of job loss, while predictive maintenance allows companies to anticipate equipment failures before they occur. This proactive approach can significantly reduce downtime and associated costs, making AI-powered robots a game changer in the manufacturing sector.
The Rise of AI in Manufacturing
In recent years, the manufacturing sector has witnessed an extraordinary transformation thanks to the integration of AI technology. This surge is not just a trend; it’s a revolution that is reshaping how products are made and how businesses operate. But what’s driving this shift? Well, several key factors are at play. First, the demand for greater efficiency and productivity in a highly competitive market is pushing manufacturers to adopt smarter solutions. Companies are no longer satisfied with traditional methods; they crave innovation that can keep them ahead of the curve.
Moreover, the advent of big data and advanced analytics has opened new doors for manufacturers. With the ability to process vast amounts of data in real time, AI systems can identify patterns and insights that were previously hidden. This capability allows manufacturers to make informed decisions quickly, reducing waste and optimizing resources. Imagine having a crystal ball that predicts your production needs and adjusts accordingly—that’s the power of AI!
Another driving force behind the rise of AI in manufacturing is the push for automation. As labor costs rise and the workforce becomes increasingly hard to manage, manufacturers are turning to AI-powered robots to take on tasks that are repetitive, dangerous, or require precision. This not only helps in cutting costs but also enhances overall workplace safety. Workers can focus on more complex and rewarding tasks, leading to greater job satisfaction and innovation.
However, it’s important to note that this shift isn’t without its challenges. Companies must invest in new technologies and train their workforce to effectively use AI tools. Additionally, the initial costs of implementing AI systems can be daunting. Yet, the long-term benefits often outweigh these hurdles, making it a worthwhile investment for many businesses. As we move forward, the manufacturing landscape will continue to evolve, driven by the relentless march of AI technology.
Benefits of AI-Powered Robots
The integration of AI-powered robots into the manufacturing sector has ushered in a new era of innovation and efficiency. These robots are not just tools; they are transformative agents that redefine how production processes are executed. One of the most significant benefits of these robots is their ability to enhance precision. Traditional manufacturing methods often suffer from human error, but AI robots operate with a level of accuracy that minimizes defects and maximizes product quality. Imagine a world where every component is crafted with impeccable detail—this is the reality that AI robots are making possible.
Moreover, the financial implications of adopting AI robots are profound. By automating repetitive tasks, manufacturers can significantly reduce labor costs. This is not just about cutting jobs; it’s about reallocating human resources to more complex and fulfilling roles. When workers are freed from mundane tasks, they can focus on innovation and problem-solving, driving the company forward. In this way, AI robots not only save money but also enhance employee satisfaction and engagement.
Another compelling advantage of AI-powered robots is their contribution to improved safety in the workplace. Manufacturing environments can be hazardous, with heavy machinery and repetitive motions leading to accidents. AI robots can take on the most dangerous tasks, protecting human workers from potential harm. This shift not only creates a safer work environment but also boosts morale, as employees feel valued and protected.
To illustrate the benefits, consider the following table that summarizes key advantages of AI-powered robots:
Benefit | Description |
---|---|
Enhanced Precision | Minimizes human error, ensuring high-quality production. |
Reduced Labor Costs | Automates repetitive tasks, allowing for workforce reallocation. |
Improved Safety | Takes on hazardous tasks, protecting human workers. |
In conclusion, the benefits of AI-powered robots extend far beyond mere operational efficiency. They represent a shift in how we think about manufacturing, blending technology with human ingenuity to create a safer, more productive, and ultimately more rewarding working environment. As we embrace these advancements, it’s clear that the future of manufacturing is not just about machines—it’s about enhancing the human experience in the workplace.
Increased Efficiency
In the fast-paced world of manufacturing, efficiency is the name of the game. AI-powered robots are revolutionizing production lines by streamlining processes, which directly translates to higher output and profitability. Imagine a factory where machines work tirelessly, optimizing workflows and minimizing downtime. Sounds like a dream, right? Well, it’s becoming a reality!
One of the key ways AI robots boost efficiency is through their ability to analyze data in real-time. They can identify bottlenecks in the production process and suggest adjustments that human workers might overlook. This capability leads to a more fluid operation where every second counts. For instance, if a robot detects that a particular machine is running slower than usual, it can alert the team to investigate before it becomes a bigger issue.
Moreover, AI robots excel at handling repetitive tasks that can bog down human workers. By taking over these mundane duties, they allow employees to focus on more complex and creative aspects of production. This shift not only enhances productivity but also improves job satisfaction among human workers, who can now engage in more meaningful work.
To illustrate the impact of AI robots on efficiency, consider the following table:
Task Type | Traditional Method | AI-Powered Method | Efficiency Gain |
---|---|---|---|
Assembly Line Work | Manual labor | Automated assembly | Up to 50% faster |
Quality Control | Human inspection | AI monitoring | Reduces error rates by 30% |
Inventory Management | Manual tracking | AI analytics | Improves accuracy by 40% |
As we can see, the integration of AI robots into manufacturing processes leads to significant efficiency gains across various tasks. The ability to work tirelessly, analyze data, and adapt to changing conditions makes these robots an invaluable asset in modern production environments. So, the next time you marvel at a perfectly manufactured product, remember the silent, efficient robots that made it all possible!
Automation of Repetitive Tasks
In the fast-paced world of manufacturing, the has emerged as a game-changer. Imagine a factory floor where machines take over the monotonous, time-consuming jobs that once drained human energy and creativity. By integrating AI-powered robots, businesses can not only boost productivity but also enhance employee satisfaction. No longer are human workers stuck performing the same tedious tasks day in and day out; they can now focus on more complex and fulfilling roles that require critical thinking and innovation.
The shift towards automation means that robots can handle various repetitive tasks with precision and speed. For instance, consider tasks like assembly line work, packaging, and quality inspections. These are areas where AI robots excel, performing with a consistency that humans simply can’t match. This not only leads to higher output but also minimizes the risk of errors that can occur due to fatigue or distraction.
Additionally, the introduction of AI robots allows for a more balanced workforce. When robots take over the mundane tasks, human employees can engage in more strategic roles, such as problem-solving and innovation. This transition not only enhances job satisfaction but also fosters a culture of continuous improvement within the organization. It’s like having a well-oiled machine where every part works in harmony to achieve a common goal.
However, it’s crucial to address the concerns that come with this shift. Employees may feel threatened by the rise of automation. To ease these worries, companies can implement training programs that equip their workforce with the skills needed to work alongside AI technologies. This creates a collaborative environment where humans and robots complement each other, rather than compete.
In conclusion, the automation of repetitive tasks through AI-powered robots is not just about efficiency; it’s about transforming the workplace into a space where creativity and innovation can thrive. As manufacturing continues to evolve, embracing this change will be key to staying competitive in a rapidly changing market.
Improved Quality Control
In the fast-paced world of manufacturing, ensuring that every product meets stringent quality standards is crucial. AI-powered robots are revolutionizing quality control processes, making them more efficient and reliable than ever before. With their ability to analyze vast amounts of data in real-time, these robots can detect defects and inconsistencies that might go unnoticed by the human eye.
Imagine a production line where every item is scrutinized with laser-like precision. AI robots utilize advanced machine learning algorithms to learn from previous data, continually improving their ability to identify potential flaws. This not only enhances the accuracy of inspections but also significantly reduces the time required for quality checks. As a result, manufacturers can achieve higher throughput without compromising on quality.
One of the standout features of AI in quality control is its capability for real-time monitoring. Traditional quality control methods often involve sampling products after production, which can lead to delays and increased waste if defects are discovered too late. In contrast, AI robots can monitor production processes continuously, providing immediate feedback and allowing for quick adjustments. This proactive approach minimizes the risk of defective products reaching the market.
Furthermore, the integration of AI in quality control fosters a culture of continuous improvement. By analyzing data trends and patterns, manufacturers can identify recurring issues and implement corrective actions. This not only boosts product quality but also enhances overall operational efficiency. For instance, if a specific machine is consistently producing defects, AI can flag this for further investigation, leading to timely maintenance and adjustments.
To illustrate the impact of AI on quality control, consider the following table that highlights key benefits:
Benefit | Description |
---|---|
Increased Accuracy | AI robots can detect defects with greater precision than human inspectors. |
Faster Inspections | Real-time monitoring speeds up the quality control process. |
Data-Driven Insights | AI analyzes data to identify trends and suggest improvements. |
In conclusion, the role of AI-powered robots in improving quality control cannot be overstated. As these technologies continue to evolve, they promise to not only enhance product quality but also drive greater efficiency across the manufacturing sector. Embracing this innovation is essential for companies aiming to stay competitive in today’s market.
Challenges of Implementing AI Robots
Integrating AI-powered robots into manufacturing isn’t all smooth sailing. While the benefits are enticing, several challenges can make this transition feel like navigating through a stormy sea. One of the most significant hurdles is the high initial investment. Setting up AI systems, purchasing advanced robotics, and ensuring that your infrastructure can support these technologies can require a hefty budget. For many manufacturers, especially smaller ones, this upfront cost can be a major barrier to entry.
Another challenge lies in the skill gap. As AI technology rapidly evolves, there’s a growing need for skilled personnel who can operate, maintain, and optimize these robots. Unfortunately, the current workforce may not be adequately trained to handle this new wave of technology. Companies may need to invest in extensive training programs or hire new talent, which can further inflate costs and complicate the integration process.
Moreover, there’s the issue of change management. Employees may feel threatened by the introduction of AI robots, fearing job loss or significant changes in their roles. This fear can lead to resistance, hampering the overall effectiveness of the implementation. To combat this, manufacturers must foster a culture of collaboration and emphasize that these robots are designed to assist rather than replace human workers. Open communication about the benefits of AI can help alleviate concerns and encourage a smoother transition.
Lastly, data security is a growing concern. With AI systems relying on vast amounts of data to function effectively, manufacturers must ensure that their data is secure from cyber threats. A breach could not only disrupt operations but also compromise sensitive information, leading to significant financial and reputational damage.
In summary, while the journey to integrate AI-powered robots in manufacturing is filled with promise, it’s essential to navigate these challenges carefully. By addressing the financial, educational, cultural, and security aspects, manufacturers can pave the way for a successful AI implementation that enhances productivity without losing sight of their most valuable asset: their people.
Future Trends in AI Robotics
The future of AI-powered robots in manufacturing is not just a trend; it’s a revolution that is reshaping the landscape of production. As technology advances at a breakneck pace, we are witnessing innovations that were once the stuff of science fiction becoming reality. With the integration of machine learning and robotics, manufacturers are poised to experience unprecedented levels of efficiency and flexibility.
One of the most exciting developments on the horizon is the rise of Collaborative Robots, or Cobots. Unlike traditional robots that operate in isolation, cobots are designed to work alongside human workers. This collaboration not only enhances productivity but also ensures that jobs are not eliminated but rather transformed. Imagine a factory floor where humans and robots share tasks seamlessly, each complementing the other’s strengths. This synergy can lead to a more dynamic and responsive manufacturing environment.
Another trend that is gaining momentum is Predictive Maintenance. AI technology is becoming increasingly adept at analyzing data from machinery to predict potential failures before they occur. This proactive approach allows manufacturers to address issues before they escalate, significantly reducing downtime and maintenance costs. Picture a scenario where a robot alerts the team about a potential malfunction, allowing for timely intervention. This not only saves money but also extends the lifespan of equipment, which is a win-win for manufacturers.
Moreover, the integration of AI in robotics is opening doors to smart factories. These facilities utilize IoT (Internet of Things) technology to create interconnected systems that communicate and optimize operations in real-time. In a smart factory, machines are not just tools; they are intelligent entities that can adapt to changes in demand, ensuring that production is always aligned with market needs. This level of adaptability is crucial in today’s fast-paced market.
As we look to the future, it’s clear that AI-powered robots will play a pivotal role in shaping the manufacturing sector. The combination of cobots, predictive maintenance, and smart factory technologies is set to redefine productivity and efficiency. Manufacturers who embrace these trends will not only stay competitive but also lead the charge into a new era of innovation.
Collaborative Robots (Cobots)
In the ever-evolving landscape of manufacturing, Collaborative Robots, or cobots, are emerging as a game-changer. Unlike traditional industrial robots that operate in isolation, cobots are designed to work hand-in-hand with human workers. This synergy not only boosts productivity but also fosters a safer work environment. Imagine a factory floor where humans and robots collaborate seamlessly, each playing to their strengths. Sounds futuristic, right? But it’s happening now!
One of the most exciting aspects of cobots is their ability to adapt to various tasks without requiring extensive reprogramming. This flexibility allows manufacturers to shift production lines quickly in response to market demands. For instance, if a company needs to switch from producing one product to another, a cobot can be easily programmed to handle the new task, saving both time and resources. This adaptability is crucial in today’s fast-paced market where speed and efficiency are paramount.
Moreover, cobots are equipped with advanced sensors and AI technology, enabling them to recognize and respond to their human counterparts. This means they can operate safely alongside workers without the need for safety cages or barriers, which are often required for traditional robots. The result? A more dynamic and efficient production environment. In fact, studies have shown that integrating cobots can lead to a 30% increase in productivity while simultaneously reducing the risk of workplace injuries.
However, the introduction of cobots also raises important questions about the future of work. Will they replace human jobs? The answer is a resounding no! Cobots are here to assist, not replace. By taking over repetitive and mundane tasks, they allow human workers to focus on more complex and fulfilling roles. This shift not only enhances job satisfaction but also encourages skill development among employees, making them more valuable in the long run.
In conclusion, collaborative robots are revolutionizing the manufacturing sector by enhancing productivity, safety, and job satisfaction. As technology continues to advance, the collaboration between humans and cobots will only deepen, paving the way for a more innovative and efficient future in manufacturing.
Predictive Maintenance
In the fast-paced world of manufacturing, downtime can be a company’s worst enemy. Enter , a game-changing approach that leverages the power of AI to foresee equipment failures before they happen. Imagine having a crystal ball that tells you when your machines are about to falter—that’s the essence of predictive maintenance! By analyzing data from various sensors and historical performance, AI can identify patterns that indicate potential issues. This not only helps in scheduling maintenance at the right time but also in avoiding costly breakdowns that can halt production.
The benefits of predictive maintenance are numerous. First off, it significantly reduces unexpected equipment failures, which can lead to massive losses in productivity. According to industry studies, companies that implement predictive maintenance can reduce maintenance costs by up to 30%! This is primarily because they can address issues before they escalate into major problems. Additionally, it allows manufacturers to optimize their maintenance schedules, ensuring that machines are serviced when truly needed rather than on a fixed schedule, which can often lead to unnecessary downtime.
But how does this work in practice? Let’s break it down into a few key components:
- Data Collection: Sensors installed on machines continuously gather data regarding their performance.
- Data Analysis: Advanced algorithms analyze this data to identify trends and anomalies.
- Actionable Insights: The AI system provides recommendations on when maintenance should be performed.
With predictive maintenance, manufacturers can also enhance their overall operational efficiency. By minimizing unplanned downtime, they can maintain a steady workflow, which translates to higher output and better profitability. Furthermore, this proactive approach fosters a culture of continuous improvement, where teams are encouraged to focus on optimizing processes rather than merely reacting to problems as they arise.
As we look to the future, the integration of predictive maintenance with other emerging technologies, such as the Internet of Things (IoT) and advanced analytics, will undoubtedly further enhance its effectiveness. The synergy between these technologies will lead to smarter manufacturing environments, where machines not only communicate with each other but also with human operators, ensuring a seamless flow of information and operations. In this brave new world of manufacturing, predictive maintenance will be at the forefront, helping businesses stay ahead of the curve.
Frequently Asked Questions
- What are AI-powered robots?
AI-powered robots are machines that utilize artificial intelligence to perform tasks autonomously or with minimal human intervention. They can analyze data, learn from experiences, and adapt to changing environments, making them incredibly efficient in manufacturing processes.
- How do AI robots improve manufacturing efficiency?
AI robots enhance efficiency by optimizing workflows, reducing downtime, and automating repetitive tasks. This means that production lines can operate at a faster pace, allowing manufacturers to increase output and profitability.
- What are some benefits of using AI in manufacturing?
Using AI in manufacturing offers several benefits, including:
- Enhanced precision: AI robots can perform tasks with high accuracy, reducing errors.
- Reduced labor costs: Automation can lower the need for manual labor, saving money.
- Improved safety: Robots can take on dangerous tasks, keeping human workers safer.
- What challenges do manufacturers face when implementing AI robots?
Some challenges include high initial costs, the need for skilled personnel to operate and maintain the technology, and potential resistance from workers concerned about job security. Addressing these challenges is crucial for successful integration.
- What are collaborative robots (cobots)?
Collaborative robots, or cobots, are designed to work alongside human workers. They enhance productivity without replacing jobs, allowing humans and robots to share tasks and collaborate effectively on the production floor.
- How does predictive maintenance work with AI robots?
Predictive maintenance uses AI algorithms to analyze data from machinery and predict potential failures before they happen. This proactive approach helps manufacturers reduce downtime and maintenance costs, ensuring smoother operations.